404
Горячие темы
764
Кроссовер Лада Азимут: знакомство и перспективы
431
Килограммы зелени: тест рамных внедорожников KGM Rexton и Tank 400
217
Представлен кроссовер Mazda CX-5 третьего поколения
183
Роскошный кроссовер Zeekr 9X: подробности
329
Трансмиссионные колики: Haval H7 и Jetour T2 в песках и на полигоне
Сейчас обсуждают

Меня никто не подменял, есть китайцы, которые интересуют и меня, есть китайцы, которым я отдаю должное, например Сяоми, который в абсолютно честной борьбе побил Тайкан на Нордшляйфе, но вот прочитав этот тест, …

Тогда бы мы вообще не читали никакие тесты. Я очень сомневаюсь, что кто-то всерьез будет рассматривать текущие поделки и по текущим ценам в качестве замены своим автомобилям.

Только полным идиотам в машине которая везет тебя, твою семью, твоих детей не важны ездовые характеристики.
А более полные лохи ещё всегда упирают на экранчики, мультимедиа на китайском с тупым переводом и беспроводные …

И чем твоя омода с жутким оскалом лучше Шкоды или Рено? Китайская дрянь которая развалится , не затормозит , не обгонит , не объедет когда нужно.

Поэтому мы и верим именно Мельникову, а не кому то там из мыла.ру.
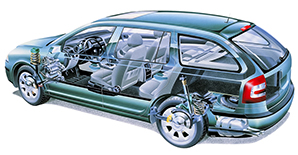
Наша экспертиза
подержанных автомобилей
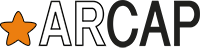
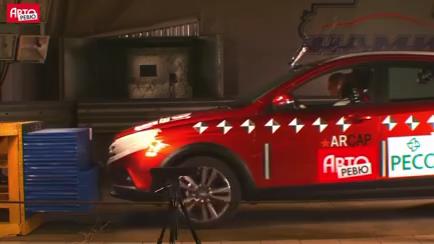
Рассылка
Лучшие материалы Авторевю — в вашем почтовом ящике
Предоставляя e-mail, вы подтверждаете свое согласие с условиями политики конфиденциальности
Парковка Авторевю
Узнайте, какие автомобили сейчас на испытаниях
Кто где?
Где работают журналисты Авторевю прямо сейчас