Репортаж из лаборатории контроля качества комплектующих калужского завода Volkswagen
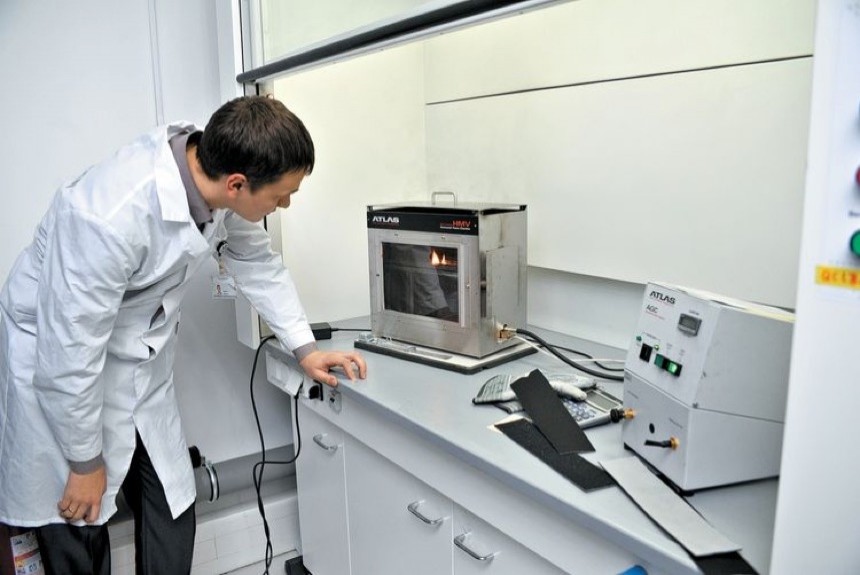
Девушка выдавливает из тюбика крем для рук - и начинает щедро обмазывать им кнопки блокировки центрального замка. Кто-то рядом сосредоточенно нюхает пластик, другой режет на куски резиновый коврик для ног. Психушка? Нет, лаборатория контроля качества комплектующих калужского завода Volkswagen. Но коридор с белыми стенами все же напоминает больницу. Да и люди здесь в белых халатах.
Обивка сидений вообще не должна гореть, а ковер на полу имеет на это право - но со скоростью не более 100 мм в минуту
Павел Советченко - laborleiter, по-нашему - заведующий. Создавать лабораторию он начал в конце 2009 года, в самый разгар подготовки к серийному производству основной модели - седана Polo (сегодня из 500 ежедневно выпускаемых здесь автомобилей на Polo приходится больше трехсот). Пока что подобной лаборатории нет ни у одного из западных производителей в России!
Места выделили с избытком - 600 квадратных метров, но многие комнаты пустуют. Пока здесь 37 установок, на закупку которых ушло более миллиона евро: спектрометры, микроскопы, компактные, размером с ванну, коррозионные и климатические камеры, разрывные машины, твердомеры, приборы для определения цвета, стойкости к ударам и к истиранию. До конца 2011 года на новое оборудование потратят еще 1 млн 600 тысяч евро, но главную проблему одними деньгами не решить. Не хватает квалифицированных специалистов.
- У вас какое образование? Немецкий или английский знаете? Не хотите у нас работать? Хорошая зарплата, бесплатная столовая, а от Калуги ходят заводские автобусы. Многие сюда перебираются семьями даже из Москвы…
Сам Павел родом из Томска, там же закончил политех, затем несколько лет проработал на заводе Volkswagen в Германии, в свои 34 года успел защитить диссертацию.
- В головной лаборатории в Вольфсбурге работает двести пятьдесят человек, а у нас пока всего девять. А задачи, в общем-то, те же.
Какие? Само собой, анализ поломок, отказов, контроль качества деталей и узлов. С просьбой провести исследования сюда обращаются разные структуры завода: испытательный центр, отдел аудита автомобилей, центр затрат.
Были, например, претензии к элементам щитка приборов именитой VDO, а на одном из столов в стороне от нашего «экскурсионного» маршрута я обнаружил бракованное заднее стекло китайской фирмы Fuyao Glass (эти стекла производят здесь же, в Калуге) вместе с заключением о несоответствии качества изготовления обогрева. Стекло меня заинтересовало неспроста: у редакционного Polo во время «пусковых» испытаний в морозильной камере лопнуло лобовое стекло той же фирмы. Случайность? Посмотрим, как другие Polo-седаны переживут первую российскую зиму.
Но чаще случаются курьезы с национальным колоритом: некоторые наши производители уже после утверждения образцов начинают втихаря халтурить, пытаясь хоть на чем-нибудь сэкономить.
- Кто? Нет, сказать не могу, хотя такое пресекали не раз. Да это все - так, текучка. Самая главная задача - отбор поставщиков и процесс доведения до ума их работы.
Каждый автомобиль Volkswagen примерно на 70% состоит из компонентов, производимых «на стороне». В Калугу приходят контейнеры из 18 стран, включая Индию, Китай и ЮАР! Однако постановление №166 о промсборке обязывает через пять лет после запуска производства доводить долю местных комплектующих минимум до 30%. Volkswagen планы перевыполняет - сейчас 41% номенклатуры деталей того же Polo (что дает целых 66% добавленной стоимости) производится в России силами 29 поставщиков. Среди них уже есть и глобальные игроки - например, Magna, Lear или Benteler (из 50 мировых топ-поставщиков в России представлены 20), но есть и «чисто российские». С ними, похоже, проблем пока гораздо больше.
Первым делом потенциальный поставщик добровольно регистрируется в заводской базе данных и, получив спецификации, вначале сам оценивает свою способность производить нужные Фольксвагену компоненты. По силам? Тогда сотрудники VW анализируют качество и цену продукции, условия производства, регулярность поставок... По итогам такого аудита в 2010 году от ворот поворот получили 113 из 191 соискателя! Глава Фольксваген Груп Рус Дитмар Корцеква лишь разводит руками: «Российские поставщики хотят очень быстро заработать очень большие деньги, но они не выдерживают конкуренции ни по качеству, ни по цене». Да-да, даже с учетом транспортных расходов и растаможки импортные детали иной раз оказываются до 30% дешевле, чем просят наши коммерсанты, - в России Volkswagen вынужден покупать детали дороже, чем где-либо в мире!
А из 78 компаний, которые в прошлом году все же прошли «входной контроль», продукцию без замечаний смогли поставлять только две! Что делать с остальными? Начинается методичная, с возвратом поставщикам для доработки, проверка материалов или деталей (наиболее ответственные компоненты проходят и через лабораторию в Вольфсбурге).
Но многим пока не суждено приблизиться к конвейеру. Например, размещенное в Калуге штамповочное производство Gestamp продолжает прессовать для Фольксвагена только импортный прокат, а всего в производстве используется меньше 5% нашей стали (для сравнения: даже в производимых в Индии Фольксвагенах вся сталь местная). И не то чтобы нет желающих поставлять российский металл, просто он не отвечает требованиям (кстати, ни одна российская компания не входит в список 10 лучших производителей стали в мире). В первую очередь, из-за низкой стойкости к коррозии: с вашим металлом, говорят, можно забыть о 12-летней гарантии от сквозной коррозии кузова! Но если российские металлурги и начнут поставлять прокат в Калугу, то внешние кузовные панели из нашего металла появятся в последнюю очередь: у немцев жесточайшие требования к так называемым оптическим свойствам поверхности - на них влияют шероховатость и пористость.
Немногим лучше дело обстоит и с полимерами: планируется, что в каждом калужском Polo должно быть использовано около 70 кг местного пластика, но пока удалось обеспечить лишь чуть больше половины этого количества…
- Результаты испытаний российских полимеров показали, что у нас умеют делать только полиуретан да, с грехом пополам, полиэтилен - сокрушаются в Калуге. - А из тридцати представленных разными производителями образцов полипропилена и полиамида мы сразу, без доработки, можем использовать только два. В итоге подошел лишь один поставщик из семи.
А ведь многие потенциальные поставщики были свято уверены в качестве своих материалов! Но при «долгоиграющих» испытаниях в калужской лаборатории начинаются сюрпризы.
На столе возле климатической установки для искусственного старения лежит потолочная ручка - вся в трещинах. Рядом - рассохшийся пластиковый кожух комбинации приборов, еще какие-то детали… Как это знакомо по отечественным автомобилям!
Выяснилось, что в России никто даже не проверял полимеры на эмиссию запаха, выцветание, растрескивание, климатическое старение… Хотя все это содержится в требованиях Фольксвагена! Поставщики пеняют на то, что в России просто негде это сделать, нет современных лабораторий! С другой стороны, кто мешает обратиться в европейские центры, как, например, поступили нижнекамские шинники, когда не смогли ответить на вопрос о старении шин Кама через три-четыре года? Кстати, проведенные в Германии тесты на стойкость резины к озону выявили проблемы, которые пришлось устранять.
Мне протягивают стеклянную банку с какими-то серыми обрезками.
- Это ковровое покрытие. Мы его подержали два часа при восьмидесяти градусах, а вы теперь понюхайте... Чувствуете неприятный запах?
Если честно, я не почувствовал.
Ерунда? Да здесь даже резиновые коврики проверяют на разрыв! Если интересно, то вырезанная из коврика трехмиллиметровая полоска должна рваться при усилии не менее восьми килограммов. А ремень безопасности обязан выдерживать без малого три тонны! Так что если не будет другого выхода, можете смело использовать его как буксирный трос.
В соседней лаборатории занимаются цветометрией, и путь дальтоникам сюда заказан. Некоторые детали, например, поставляемые фирмой Magna бамперы, приходят на завод уже окрашенными - и для выявления возможного «разнотона» нужен глаз художника.
Под лампами, дающими свет разного спектра, лежат три черные пластины: «Видите, образцы ведь выглядят одинаково? А теперь (свет переключается) опытный глаз уже заметит разницу, а если так (еще щелчок), то уже трудно не заметить, что пластины разного цвета. Правда?».
Правда! Кстати, имейте в виду, что в дилерских шоу-румах обычно используется «холодное» освещение (сool white). Хитрость в том, что при таком освещении выявить «разноцвет» крайне сложно, поэтому машину - особенно после ремонта! - нужно обязательно осматривать на солнце, причем лучше всего на закате.
Кузовной лак BASF из Павловского Посада подвергают более суровой пытке. На свежеокрашенных пластинах ножом делается Х-образный надрез до краски (не потому ли, что с этой буквы начинается любимое слово вандалов, царапающих машины?) - и теперь лак пытаются оторвать специальным суперлипким скотчем. Не получилось? Тогда обдаем струей кипятка из Керхера. Все еще держится? Но под обстрелом килограммом дроби из агрегата с труднопроизносимым названием гравилометр (который Павел ласково называет «голубым слоном») не устоит ни один лак! И тут уже оценивают степень отслоения и плотность появившихся «оспин».
Похожим образом проверяются фары и задние фонари (кто не в курсе, их поверхность тоже покрыта лаком). Кстати, у проходящего наш ускоренный ресурсный тест калужского Polo (первый отчет - в одном из ближайших выпусков Авторевю) за 10 тысяч километров прозрачные колпаки рязанской головной оптики Automotive Lightning заметно «отпескоструились» и помутнели. Павел, а не пора ли рязанским фарам еще раз пообщаться с «голубым слоном»?
Да, чуть не забыл: так зачем же на клавиши электрооборудования наносят крем для рук, а попутно - еще и лосьон для загара? Обработанные косметикой кнопки заворачиваются в марлю и сутки хранятся при 80°С - так проверяют стойкость пиктограмм и лакового покрытия поверхности (для верности его предварительно еще и царапают). Косметика фирмы Thierry из Штутгарта, правда, не обычная, а концентрированная - на тюбиках даже есть предупреждение об опасности использования содержимого по прямому назначению. Или это - хитрость, чтобы крем быстро не заканчивался?
Некоторые локализованные компоненты автомобилей Volkswagen российского производства |
|
Продукция |
Поставщик |
Штамповка | СП «Гестамп-Северсталь-Калуга» (Gestamp Automocion), Калуга |
Бамперы, крышки топливного бака | ЗАО «Магна Технопласт» (Magna International Inc.), Калуга, Санкт-Петербург и Нижний Новгород |
Базовые эмали и лаки | ООО «Басф Восток» (BASF SE),Павловский Посад, Московская область |
Колеса из легких сплавов | ООО «КиК», Красноярск |
Шины | ОАО «Нижнекамскшина», Нижнекамск |
Шины | ОАО «СИБУР-Русские шины», Ярославль |
Воздушные фильтры в сборе с корпусом | Компания «Big Filter», Санкт-Петербург |
Элементы тормозной системы | ООО «Прогресс» (TI Automotive Russia), Санкт-Петербург |
Топливные баки | ООО «ЯПП Рус Автомобильные системы» (Yapp Automotive Parts Co. Ltd), Калуга |
Выхлопные системы | ООО «Теннеко Аутомотив Волга» (Tenneco Inc.), Санкт-Петербург |
Элементы подвески | ООО «Бентелер Калуга» (Benteler AG), Калуга |
Светотехника | ООО «Аутомотив лайтинг» (Bosch Automotive Lightning и Magneti Marelli Spa), Рязань |
Стекла | ООО «Фуяо-Калуга» (Fuyao Glass Industry), Калуга |
Наружные зеркала заднего вида и пластиковые элементы салона | ООО «Автокомпонент», Нижний Новгород |
Сиденья | ООО "Лир» (Lear Corporation), Калуга и Нижний Новгород |
Обивка кресел | СП «Превент Иммобилиен Рус» (Prevent Grоup), Озеры, Московская область |
Панели приборов | ООО «Континентал Аутомотив РУС» (Continental Automotive Systems), Чистополь |
Компоненты электросети | ЗАО «Микротех» (Microtech Group), Калуга |
Жгуты проводов | ОАО «Роберт Бош Саратов» (Robert Bosch GmbH), Энгельс |
Элементы внутренней отделки | ООО «Форесия Аутомотив» (Faurecia Group), Калуга и Санкт-Петербург |
Элементы внутренней отделки | ООО «Вистеон Рус» (Visteon Corporation), Калуга |
Элементы отделки багажника и пола | ООО «ХП Пельцер РУС» (HP Pelzer Group), Калуга |
Полимеры | СП «Изопласт Системс» (Isoplast-Systems Rus), Калуга |
Элементы внутренней отделки | ООО «Группа Антолин Санкт-Петербург» (Grupo Antolin), Санкт-Петербург |
Механизмы крепления и регулировки деталей интерьера | ООО «Шердель Калуга» (Scherdel GmbH), Калуга |
Шумоизоляция и элементы обивки салона | ООО «Трамико» (Tramico SAS), Ставрово, Владимирская область |
Химикаты | ООО «Хеметалл» (Chemetall GmbH), Москва |
Полимеры | Proseat GmbH, Москва |
Резинотехнические изделия | ООО «Анвис Рус» (Anvis Group), Тольятти |
Материалы для окраски | ООО «Дюпон-Русские краски» (E.I. du Pont de Nemours and Company), Ярославль |
Смазочные материалы | ООО «Фукс Ойл» (Fuchs Petrolub AG), Ярославль |
Уплотнения | ООО «Сааргумми-Русланд» (Saargummi Group), Ярославль |
Звуковые сигналы | ЗАО ЛЭС, Лысково, Нижегородская область |