В обозримом будущем — шесть миллионов! Как производят шины Viatti
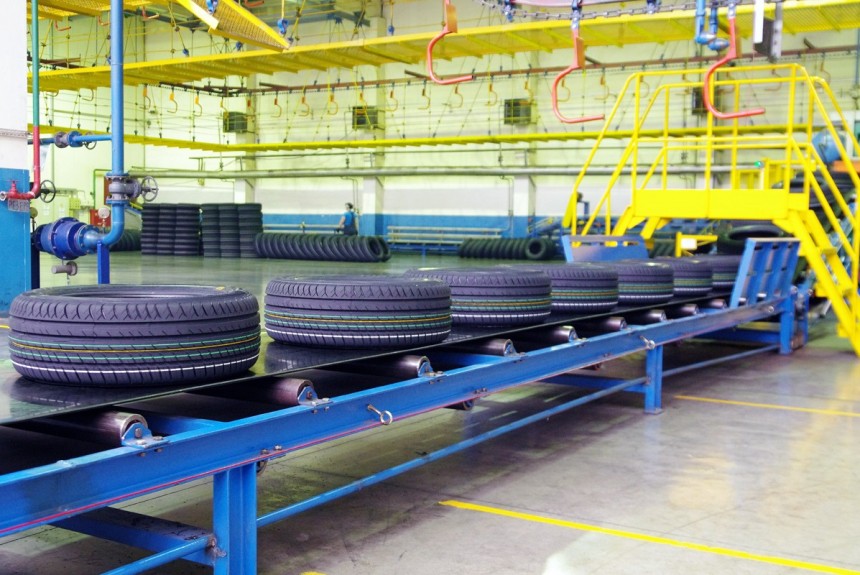
История бренда совсем молода. Чтобы ее поднять, вовсе не нужно глубоких изысканий. Все началось в начале 2000-х, когда комплекс предприятий ПАО «Нижнекамскшина» перешел под крыло ПАО «Татнефть». Позже руководство материнской компании поставило задачу — наладить выпуск легковых шин, соответствующих мировым стандартам надежности и безопасности и не уступающих по своим характеристикам зарубежным аналогам.
Здание Управляющей компании «Татнефть-Нефтехим» и территория завода ПАО «Нижнекамскшина»
Для этого потребовалось не просто переоснастить завод, закупить новейшее оборудование, но и создать на основе конструкторского бюро советского типа собственный современный Научно-технический центр (НТЦ). На сегодняшний день НТЦ «КАМА» ведет не только все разработки шин — от проектирования до запуска в производство, но и занимается строжайшим отбором и омологацией комплектующих российских и зарубежных поставщиков.
При проектировании покрышек Viatti были использованы как имевшиеся собственные наработки, так и опыт сотрудничества с известными шинными брендами, в том числе иностранными. Новая линейка получилась аутентичной, уникальной, не имеющей аналогов по прочностным характеристикам, способной на равных конкурировать с зарубежной продукцией в доступном ценовом сегменте.
Шина Viatti
С 2009 года Viatti используют как шины первичной комплектации на российских предприятиях зарубежных автоконцернов — соотношение цена/качество было по достоинству оценено не только конечными потребителями, но и европейскими компаниями. Например, продукция нижнекамского завода поставляется на автозавод Volkswagen в Калуге, Ford-Sollers в Елабуге.
Но вернемся к заводу, который внешне отличается от зарубежных шинных производств, построенных в России за последние годы. Если они чаще всего представляют собой один огромный цех, то для выпуска Viatti использовали уже имеющиеся цеха ПАО «Нижнекамскшина», только тщательно реконструированные. Например, под новейший комплекс по выпуску резиновых смесей – основ шинного производства – высоту стен пришлось значительно увеличивать. Также для оснащения завода Viatti было закуплено оборудование, идентичное или аналогичное тому, что используют многие международные шинные производители.
Общий вид производственной площадки подготовительного цеха
От состава резиновой смеси зависят эксплуатационные характеристики будущей шины, именно поэтому каждый из компонентов — натуральный и синтетический каучук, технический углерод, химикаты — играет особенную роль при ее изготовлении. Для каждой модели шин — своя резиновая смесь. Ее состав, как и у всех шинников, фирменное ноу-хау.
Загрузка компонентов резиновой смеси, их смешение при определенной температуре и вальцевание в ленты происходят в одном цехе. Процесс полностью автоматизирован. Всем управляют несколько операторов, отслеживающих через мониторы соблюдение технологических режимов и в случае необходимости запускающих те или иные рецептуры.
Склад хранения готовых резиновых смесей в подготовительном цехе
Система контроля на заводе Viatti не менее строгая, прямо скажем, чем в любом Шереметьево или Хитроу. Прежде чем шина попадет на склад, ей предстоит пройти комплекс испытаний — от проверки геометрических параметров шин и статического дисбаланса до сканирования на рентгеновской камере, которое выявляет любые неточности, образованные в том числе и во время сборки. Также проводится дополнительная проверка на предмет четкости маркировок, наличия царапин и других визуальных дефектов шины — подобные «недостатки» продукции считаются браком.
Узел автоматической загрузки/выгрузки шин установки для рентгенодефектоскопии легковых и легкогрузовых шин
Шинный конвейер все же отличается от автомобильного, прежде всего разнообразием ассортимента, который может выпускаться на одной линии, и гибкостью, — для этого его перенастраивают под каждую модель и типоразмер. Впрочем, в условиях современных компьютерных технологий переналадка технологической карты — дело недолгое. Тем не менее для каждой из восьми моделей, включая и легкогрузовые, должны быть сделаны оригинальные каркасы, брекеры, протекторы и боковины — кстати, с переменным распределением жесткости.
Такая технология, именуемая VRF (Variable Rigidity of a Framework), адаптирует шину под характер дорожного покрытия. Среди широко применяемых — Hydro Safe S для вывода воды из пятна контакта, SnowDrive, призванная улучшить проходимость в глубоком снегу, скошенные плечевые зоны для эффективного вытеснения снежной каши. Beveled Border (BB), асимметричный рисунок протектора Asymmetrical Design (AD) и многие другие. Цель — сделать любую из моделей Viatti максимально безопасной и надежной.
Вообще, чтобы пройти по всем постам завода, понадобится немало времени. Все они соединены либо транспортерными лентами, либо подвесными конвейерными линиями, перемещающими более 30 тысяч шин в день. Для таких объемов выпуска разработаны самые современные и быстродействующие схемы.
Подвесной конвейер для транспортировки «сырых» шин
Конвейерная лента с шинами размера 215/55 R17 94V V-130 на участке инспекции качества на линии
У готовой продукции Viatti весьма приличный заявленный эксплуатационный ресурс. Для летних моделей до 50 тысяч километров, для зимних три—четыре сезона с учетом нагрузок и климата. Особенность почти всех моделей Viatti в применении смешанного корда, включающего как текстильные, так и металлические нити. Благодаря этому проектировщики гарантируют безопасность и особую прочность такой конструкции как на российских дорогах, так и на европейских.
Бобина с нейлоновой нитью (мононитью)
Весь процесс интеграции разнообразных заготовок с кордовыми составляющими опять же обходится практически без участия людей. Для каждого элемента шины свой станок. На выходе будет сложный продукт с разнообразными физическими свойствами, после вулканизации которого получается готовая шина.
Знакомые с зарубежным шинным производством вряд ли удивятся обилию роботизированных манипуляторов и компьютеров. Все лучшее, что существует в мировой шинной отрасли, было установлено в Нижнекамске. И если только в развитие НТЦ за последние годы было вложено порядка 400 млн рублей, то инвестиции ПАО «Татнефть» в производство куда серьезнее.
Прикатка протектора на сборочном комплексе
Участок с барабанными сборочными станками — один из наиболее зрелищных на линии. Невулканизированный многослойный каркас шины оказывается на нагретом вращающемся барабане, меняющем свою геометрию. Затем цилиндрический каркас сжимается по бокам, обрастает силовыми элементами и протекторной лентой, после чего отправляется на формовку и вулканизацию.
Для каждой модели и типоразмера своя форма обжимной матрицы, причем специалисты различают шины вовсе не по торговым названиям, а по внутризаводским индексам. Так удобнее и правильнее с технологической точки зрения. Например, Viatti Bosco A/T больше известна как V-237, а шина для легких грузовиков Viatti Vettore Inverno — как V-524.
Выставочная экспозиция шинной продукции ПАО «Нижнекамскшина»
Шинное производство в Нижнекамске 45 лет служит локомотивом отечественной шинной отрасли. Первые подобные предприятия создавали технологическую основу российской промышленности в этой сфере. Сейчас нижнекамская продукция поставляется уже не только на автомобильные заводы российских марок, но и на предприятия мировых автоконцернов. Бренд Viatti — это новый этап в истории производства, который аккумулирует в себе весь опыт и мировые стандарты качества, при этом продукция Viatti остается надежной и доступной широкому кругу российских и зарубежных потребителей.