Английская сборка: как делают двигатели Ingenium для автомобилей Jaguar?
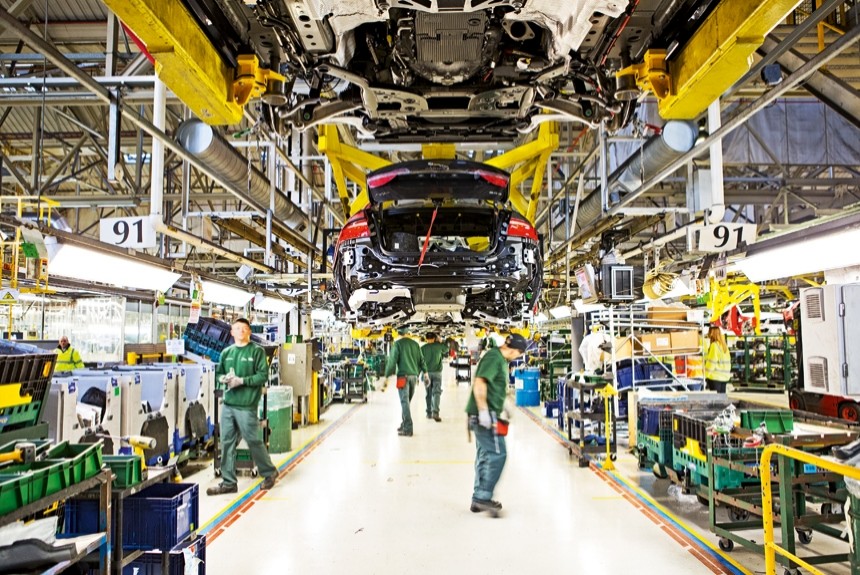
Ford продал индийскому миллиардеру Ратану Тате британскую компанию Jaguar Land Rover еще в 2008 году, но переход на собственные силовые агрегаты затянулся — даже новейший седан Jaguar XE вышел в свет с фордовским бензиновым двигателем EcoBoost. И только теперь его сменит новая «четверка» собственного семейства Ingenium — рожденная здесь, в Англии.
Семейство моторов Ingenium инженеры исследовательских центров Jaguar Land Rover в Уитли и Гэйдоне разрабатывали c 2011 по 2014 год не без участия известных фирм AVL и Ricardo. Инвестиции — 250 миллионов фунтов стерлингов. В конструкции — никаких революций: турбонаддув, непосредственный впрыск, цепной привод газораспределительного механизма (ради снижения шума звездочка коленвала не идеально круглая, а эллиптическая — «приплюснутая» на полмиллиметра). Причем, как и у коллег из BMW и Volvo, семейство Ingenium — модульное. Бензиновые и дизельные агрегаты идентичны на три четверти и основаны на блоках из алюминиевого сплава со схожими диаметром цилиндра, ходом поршня, межцилиндровым расстоянием и рабочим объемом цилиндра в 500 «кубиков». Как и у последних моторов BMW, ради снижения потерь на трение распредвалы имеют роликовые подшипники, а шумоизоляция установлена прямо на моторе: так ее требуется меньше.
Возможное количество цилиндров — от трех до восьми, что должно закрыть все потребности модельного ряда британской марки. Но это в будущем.
Пока же половина парковочных мест для сотрудников новенького завода, построенного прямо в чистом поле в пригороде Вулверхэмптона, пустует. В строительство этих цехов площадью около 100 тысяч квадратных метров с 2012 года вложено 500 миллионов фунтов стерлингов. Почему выбрали именно это место в графстве Уэст-Мидлендс? Потому что из Вулверхэмтона меньше часа езды до каждого из трех автосборочных заводов компании — в Солихалле, Касл Бромвиче и Халвуде.
Сейчас работает лишь один сборочный цех — из всего унифицированного семейства AJ200 с начала 2015 года здесь ежедневно выпускают не более 600 четырехцилиндровых дизелей AD20D4 (163—180 л.с.), знакомых нам по автомобилям Jaguar ХЕ, XF и модернизированному кроссоверу Range Rover Evoque. Заглядываю в соседний цех — тишина: бензиновую турбочетверку AD20P4 начнут делать только этим летом, а пока идет отладка технологической цепочки.
Порядок и чистота — идеальные! Линии по изготовлению коленвалов, головок и блоков цилиндров автоматизированные: всего 50 рабочих присматривают за оборудованием марок Alfing, Nag, Niles-Simmons. Геометрия деталей проверяется автоматически, но для верности несколько образцов из каждой партии исследуются в лаборатории.
Собственно сборкой двигателя занимаются без малого 200 человек — но ручной труд применяется только на операциях, где практически невозможно ошибиться (таких — 180 из 210 тактов конвейера). А автоматизированы, к примеру, не только нанесение герметика и установка коленчатого вала, но и монтаж поршней. На выходе каждый готовый двигатель проверяют «холодной» обкаткой (здесь контролируют компрессию, давление масла, функционирование всех систем и датчиков) и «горячей» работой (моторы гоняют по четыре минуты). В цехе сборки хватило места даже четырем моторным стендам: двигатель из каждой партии испытывают по 50 часов в сборе с коробками передач — для этого рядом хранят все возможные варианты трансмиссий.
Готовые моторы, упакованные в ящики, грузят в фуры и отправляют на один из трех автосборочных заводов компании Jaguar Land Rover. И я еду следом! 30—40 минут неспешных дорожек — и мы оказываемся в городке Касл Бромвич.
Знаете, что общего между автомобилями Jaguar и самолетами Spitfire? Спорткупе F-Type, седаны XF и частично XE делают на том самом заводе под Бирмингемом, со стапелей которого сошла бо́льшая часть знаменитых британских истребителей времен Второй мировой. Их делали вплоть до 1946 года!
Об историческом прошлом сегодня напоминают только стела перед въездом и корпуса цехов из потемневшего кирпича. Линия сборки кузовов точь-в-точь как та, что я видел в Солихалле, где производят большинство седанов Jaguar XE. Пять сотен сва... то есть клепочных роботов! Вместо сварочных клещей у них специальные «струбцины»: алюминиевые панели ягуаровских кузовов скрепляются несколькими тысячами заклепок двух десятков типов. А еще есть роботы с дозаторами для нанесения на кузовные швы сотен метров специального синтетического клея, окончательно застывающего в сушильной камере после окраски кузова.
Короткий коридор будто кроличья нора из английской сказки: после царства роботов соседний цех сборки седанов XF, ежедневно выдающий до 500 машин, — словно из другой эпохи! Исторический дух, или, если угодно, традиционный британский консерватизм, витает повсюду. Бо́льшая часть операций, включая вклейку стекол, производится вручную, салон рабочие собирают без монтажных кресел, а при навеске дверей, как и 30 лет назад, используют молоток. На этом фоне полностью роботизированная «свадьба» кузова с силовым агрегатом выглядит просто космической технологией.
И даже не припомню, где еще качество своего труда проверяют сами рабочие, причем замечания пишутся на обычный бумажный листок на стене. На выходе после проверки электроники британцы тестируют машины только в дождевальной камере и на беговых барабанах: своего испытательного трека у завода нет.
А еще я было принял за тонкий английский юмор форменную одежду экспресс-доставки DHL на водителях электропогрузчиков с запчастями, безостановочно снующих между сборочными постами. Однако оказалось, что это настоящий персонал DHL: на рабочих этой компании-подрядчика приходится 700 человек из 4500 сотрудников всего завода! Отдали внутренние перевозки, что называется, на аутсорсинг.
Но двигатели у англичан теперь собственные. Бензиновый Ingenuim на седане ХЕ мы увидим не раньше 2017 года, а жаль. Не терпится проверить, лучше ли он уживется с «автоматом», чем фордовский EcoBoost?