Почему у Audi A8 нового поколения будет самый тяжелый кузов за всю историю модели?
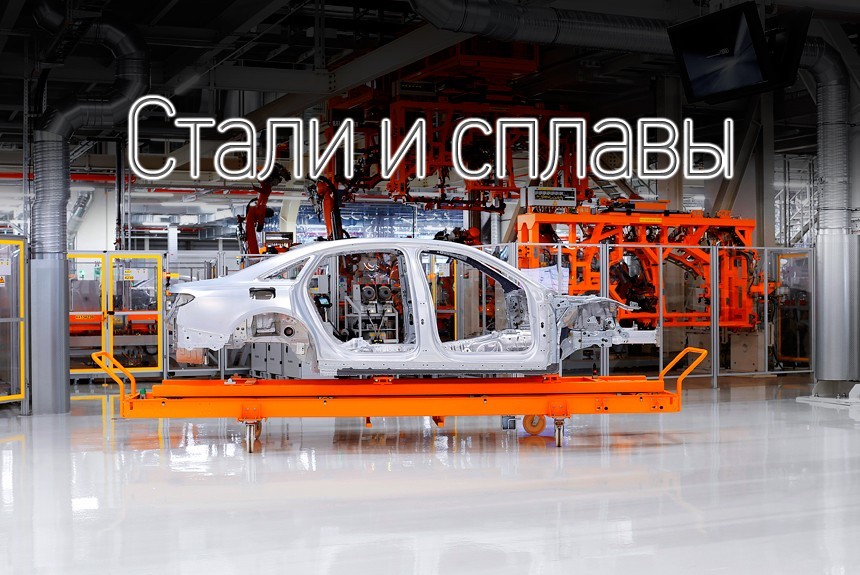
Алюминиевый кузов — визитная карточка всех поколений флагманского седана Audi А8. И для грядущей «восьмерки» серии D5 эту визитку не просто переиздали, а сделали на совершенно ином полиграфическом уровне.
А ведь совсем скоро массовой автомобильной алюминизации исполнится уже четверть века! Конечно, многие экспериментировали с крылатым металлом еще в начале двадцатого столетия, да и в 30-х те же первые «властелины колец», гоночные Auto Union, чего стоили. И все же именно появившийся в 1994 году Audi А8 первого поколения (серии D2) стал пионером — крупносерийным автомобилем, у которого из алюминия было сделано не только оперение, но и силовая структура несущего кузова ASF (Audi Space Frame).
Без навески кузов Audi А8 D2 из алюминиевых штамповок, профилей и отливок, практически повсеместно соединенных только сваркой, весил всего 249 кг — почти вдвое меньше стального тех же габаритов. А потому и в целом Audi A8 вышел менее увесистым, нежели главные соперники — тогдашние «семерка» BMW и Mercedes S-класса.
Самый легкий и самый ажурно-лестничный кузов был у «восьмерки» серии D3
Когда в 2003 году на алюминий всерьез положили глаз и англичане из фирмы Jaguar, немцы вовсю уже не только варили, но и клепали кузова следующего Audi A8 серии D3 образца 2003 года, которые весили всего 220 кг! И собирались из более крупных модулей: например, полноразмерной средней стойки.
У появившейся в 2010-м предыдущей «восьмерки» третьего поколения (серии D4) основу средней стойки в угоду требованиям безопасности пришлось делать уже из высокопрочной стали. Кузов чуть потяжелел (до 231 кг), но стал заметно жестче и прочней.
У нынешнего Audi A8 стальные средние стойки соединяются с соседними алюминиевыми деталями с помощью болтов и клея. Стянуты ими и съемные фронтальные части коробов полностью алюминиевых передних лонжеронов — для облегчения ремонта
А у грядущего Audi А8 поколения D5 кузов будет… самым тяжелым за всю историю семейства! Без навески — 281 кг. Ведь если у предыдущей «авоськи» тело состояло из алюминия на 92%, то у новой — только на 58%. А около 40% придется на... сталь. Высокопрочную и обычную.
Конец «крылатой» традиции?
В новом Audi А8 поколения D5 между чашками передней подвески — прикрученная пустотелая и ажурная внутри распорка из магниевого сплава. Такая еще на 28% легче и на 33% прочней алюминиевой
Распорка между литыми алюминиевыми чашками передней подвески впервые сделана из еще более легкого и прочного магниевого сплава. А вслед за мультиматериальным BMW седьмой серии, где в качестве локальных усилителей используются композитные элементы, и в кузове А8 появился углепластик: из него единой деталью сделаны задняя стенка салона и полка под стеклом. Смысл не только в облегчении: именно эти элементы берут на себя треть обязанностей по сопротивлению скручиванию кузова. Кстати, полезней всего сие новшество для самой уязвимой длиннобазной версии с панорамной крышей: ее жесткость возросла аж на 24%.
Стальная энергопоглощающая «лобовая броня» сборного моторного щита, высокопрочные сплавы боковых стоек, порогов и рамки ветрового стекла призваны повысить безопасность. Причем не только пассажиров: намного надежней, чем сейчас, будет защищен и аккумуляторный блок у гибридной версии.
Такого количества материалов в кузове Audi A8 еще не было
В итоге кузов у Audi A8 серии D5 превратился в винегрет из трех десятков разновидностей материалов. Причем если в кузове нынешней «восьмерки» тринадцать алюминиевых сплавов, то у грядущей — двадцать, семь из которых уникальные, разработанные cпециально для Audi. А любой крупный узел, будь то моторный щит, пол или стойки, похож на слоеный пирог с начинкой из нескольких металлов. Говорят, такая конструкция даже потребовала разработки специальной методики утилизации с чуть ли не подетальным расчленением, ведь если алюминиевые сплавы легко перерабатываются, то с высокопрочными сталями все иначе.
Такие острые грани у алюминиевых деталей стали доступны дизайнерам только благодаря специальному особо пластичному сплаву и многоступенчатому формованию
Чертовски сложно! Наверняка очень дорого. И максимально неудобно в восстановлении. Ведь только для того, чтобы сшить это лоскутное одеяло, нужны восемь видов сварки (в том числе лазерная), десятки вариантов заклепок и специальные саморезы, одетые в полимерную изоляцию для предотвращения электрохимической коррозии. Еще — сотня метров соединений при помощи особого изолирующего клея (он твердеет при сушке кузова), фиксирующее тиснение, пуклевка (это когда давлением один слой металла плющится и зацепляется за другой). А для облицовки алюминиевой штамповкой порогов и стоек вместо заклепок придумали использовать забортовку кромки — так можно уменьшить фланцы и сделать дверные проемы шире.
Чтобы воплотить этот кошмар технолога в массовое производство, немцы вложили два миллиарда евро! Для сравнения: это раза в три больше, чем стоил весь калужский завод Volkswagen.
Кипенно-белая стерильность полов рождает ощущение операционной. Разве что диодное освещение не слишком яркое, но роботам оно и не нужно! Ведь на 50 тысячах квадратных метров площади нового кузовного цеха в Неккарзульме их полтысячи. А 500 рабочих делают только 15% операций — да и те, за исключением навески дверей с капотами, из разряда «подай-принеси».
Одно из самых технологически сложных соединений именуется Gtip punch-riveting (обведено): когда заклепка пробивает два материала и «вязнет» в третьем
Я помню красоту этого зрелища по такому же роботизированному ягуаровскому «алюминиевому» кузовному цеху в Солихалле. А теперь утвердился в том, что бесконечно смотреть можно не только на огонь и воду, но и на дистанционную лазерную сварку — когда космический бластер с системой зеркал микрозигзагами вычерчивает сложнейшую трехмерную траекторию в 20 см от поверхности, вызывая на ней огненный шквал. Завораживает.
В этом стапеле (на заднем плане) кузов собирается в единое целое. Смещение боковин по всем осям не превышает 0,2 мм!
Роботы Kuka с рабочими инструментами Böllhoff живут своей жизнью — вплоть до того, что сварочные и «клепочные» клещи смышленые механические руки меняют себе сами. Даже не верится, что они могут ошибаться, — но контроль качества все равно строгий. Вдобавок к оптической проверке поверхностей все без исключения кузова проходят через лазерный стенд, где их геометрия контролируется по двум тысячам точек. Впрочем, это дело давно привычное при производстве многих автомобилей. А вот чтобы кузовам делали УЗИ… Да-да, и предварительно сбрызгивают «тело» специальной жидкостью. На самом деле это из области не медицинских, а авиатехнологий: так проверяют структуру клеевых швов — ведь клей поглощает ультразвук, а при его отсутствии сигнал возвращается обратно в приемник.
Так выглядит лазерная головка с системой зеркал для лазерной сварки алюминиевых сплавов
Пока в Неккарзульме заканчивают работу в тестовом режиме, производя кузова для предсерийных экземпляров «восьмерки» D5. А узнать, изменился ли характер Audi A8 четвертого поколения столь же серьезно, как и его кузов, мы сможем через несколько месяцев: дебют ожидается в июле нынешнего года.