Подшипники на японском заводе NTN-SNR: как сочетаются традиции и современность
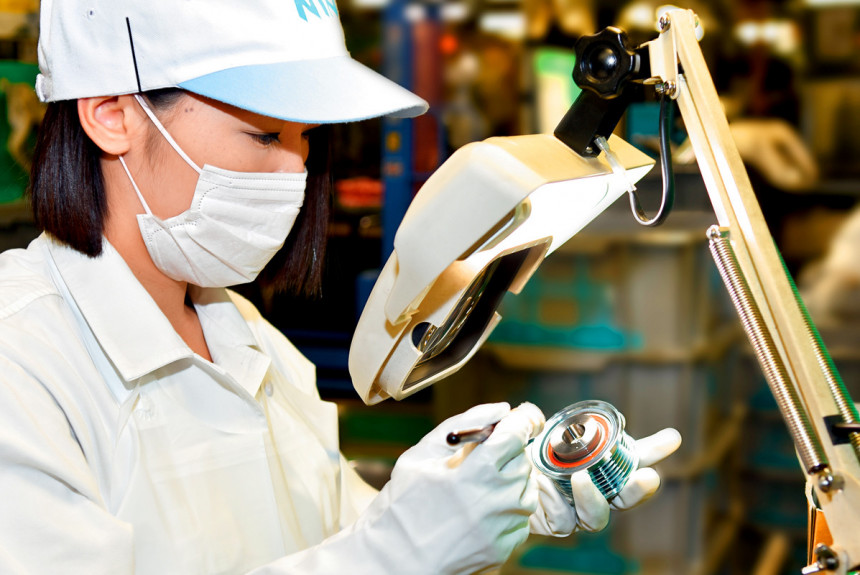
Пять веков назад Леонардо да Винчи нарисовал подшипник качения с сепаратором для шариков. Сейчас он был бы рад за свою идею — например, в современной легковушке около 150 шарикоподшипников. А на заводе альянса NTN-SNR в японской Ивате, где я побывал, они выпускаются миллионами!
История французской компании SNR началась с того, что в 1880 году в руки кузнеца Жака Шмидта из пригорода Цюриха случайно попал подшипник. А вместе с ним, как оказалось, и удача: кузнец умудрился наладить небольшое производство — и сперва швейцарские сельхозпроизводители стали использовать подшипники Шмидта на жнейках, затем последовал первый оптовый заказ от цюрихских трамвайщиков. И лавинообразный рост потребности для грузовиков и самолетов перед Первой мировой — дела пошли так, что к 1918 году экс-кузнец вместе с сыном расширились и отстроили собственный новенький завод SRO во французском местечке Аннеси.
Далее были разрушительная бомбежка союзниками в 1944-м, приобретение остатков завода только что национализированной компанией Renault и переименование его в SNR (Sociеtе Nouvelle de Roulements), то бишь «Новая подшипниковая компания». Подшипниками SNR оснащались Citroen 2CV и Renault 4, сверхзвуковой Сoncorde и Airbus А380, формульный болид Renault Алена Проста и раллийные Ситроены…
Старт японской фирмы NTN (ее название, кстати, происходит от имен основателей Нобору Нивы и Джиро Нишизоно) был и того интереснее: в гавани Кобе возьми да и затони груженное подшипниками шведское судно. Предприимчивые японцы купили груз на аукционе страховой компании, отмыли, вновь смазали — и продали «утопленников» как новеньких. А затем, в том же самом 1918 году, начали производство собственных подшипников. Следом — тоже бурный рост благодаря милитаризации и спад в конце 40-х. А в 60-х снова расцвет: у немецкой фирмы INA японцы приобрели технологию производства игольчатых подшипников, у британской Hardy Spicer — шарниров равных угловых скоростей (ШРУСов), были созданы филиалы в Германии, Франции, США и Канаде. А в 2007 году NTN покупает компанию SNR — на сегодня это один из трех крупнейших инвесторов в экономику Франции.
Сейчас у альянса исчисляемые миллионами ежемесячные тиражи, семь заводов только в Японии и еще десятки — в 33 странах Европы, Азии, обоих Америках и Китае. Итого — второе место в мире после компании GKN по производству ШРУСов и третье (вслед за INA и SKF) по подшипникам. Которые, помимо автомобилей, применяются в самолетах, поездах, ветряных электростанциях, спутниках и даже медицинских имплантах.
Одна из перспективных разработок — использование роликовых подшипников вместо вкладышей коленвала. В обмен на удорожание конструкции — более легкая прокрутка, особенно в первый момент при старте
Хотя на материнском для NTN подшипниковом заводе в Ивате (70% продукции которого предназначено для автомобилей) время словно остановилось. На мгновение мне даже почудилось, будто я оказался на советском литерном ГПЗ! Вереницы зеленых станков, запах горячего масла, лязг и звон железа, механическая автоматизация... Технологии за последние лет тридцать практически не изменились. Обоймы получают ковкой и токарной обработкой, будущие шарики для шарикоподшипников сперва по-прежнему нарубают из прутков, штампуют и обкатывают. Всего процесс состоит из двух—трех десятков операций, которые круглосуточно выполняют линии по 50—60 станков — каждая под присмотром одного—двух рабочих.
После сборки подшипника машины проверяют правильность соединения деталей. Непрерывно контролируется дюжина различных параметров — включая количество шариков, шум, качество смазки, вес и систему уплотнения
Впрочем, главное — не сложность или простота процесса, а качество. Ведь я как автовладелец хочу одного — как можно дольше о подшипниках не слышать. В прямом и переносном смысле. Поэтому уплотнения и смазки в Ивате заказывают, к примеру, у японской корпорации Idemitsu, известной своими автомаслами. А едва ли не половина всех технологических операций посвящена доведению шариков, роликов и их дорожек до зеркального состояния. Причем длительность и степень обработки поверхности зависит от назначения и класса подшипника — чем точнее изготовлен подшипник, тем более высокую предельную частоту вращения он выдерживает. Всего таких классов восемь, от нормального до сверхпрецизионного: для автомобилей обычно хватает шести первых, а самые высокие используются, например, для высокоточных станков и в авиастроении.
Кстати, после финальных измерений внешней и внутренней обойм к ним автоматически подбираются шарики нужного диаметра из коллекции с шагом в десятитысячные доли миллиметра! Практически аптекарская точность — но благодаря ей у подшипников и ход ровнее, и жизнь дольше. При расчете ступичных, к примеру, закладывают начало износа не ранее чем через шесть лет — обычно пробег за это время составляет 100—120 тысяч километров.
Ну и конечно, контроль качества: все без исключения подшипники, помимо соответствия веса и размеров, проверяются на сопротивление и плавность качения. Причем дважды — в сухом виде и после наполнения рабочей смазкой.
Одна из главных операций при изготовлении подвижных деталей ШРУСов и подшипников — шлифовка. Точность для ролика подшипника — на уровне микрона. С работающей круглые сутки линией управляется всего пара рабочих
Вот соседний цех по производству ШРУСов удивил фактически единственной выходной контрольной операцией — на плавность движения узлов под разными углами. И тем, что шлицы нарезаются не в мягком металле, а уже после его упрочнения индукционной закалкой (так с большей гарантией выдерживаются заданные финишные размеры). В остальном процессы создания ШРУСов и подшипников имеют немало общего: поверхности сепаратора и обоймы тщательнейше шлифуются — и собирается весь узел внутри одного аппарата. Даже шарики в обоих случаях поступают из одного цеха. Станки, правда, на ШРУС-участках посовременнее, а большие партии приводов в сборе производят с помощью десятка роботов Yaskawa.
Важное направление развития конструкции ШРУСов — облегчение. Например, за счет крепления к ступице болтом вместо длинного шлицевого вала и гайки
Но есть из общего и кое-что поважнее. Ни для ШРУСов, ни для подшипников у NTN-SNR нет разных «сортов» для поставок на конвейеры автопроизводителей и в магазины запчастей. И, главное, нет разницы в качестве деталей в коробках с логотипами автопроизводителей и своими собственными — коли они предлагаются в качестве аналогов. Причем неважно, откуда они на нашем российском прилавке родом: из Японии, Франции, Германии или даже Китая, — на всех заводах альянса NTN-SNR стандарты качества единые. Судя по заводу в Ивате, вне зависимости от возраста станков.
Более отдаленное будущее тоже предполагается крупномодульным: электрический колесный мотор-генератор интегрирован в один узел со ступицей и подшипником