Немаленький NMUK: Илья Хлебушкин примерил униформу рабочего на заводе Nissan в Сандерленде
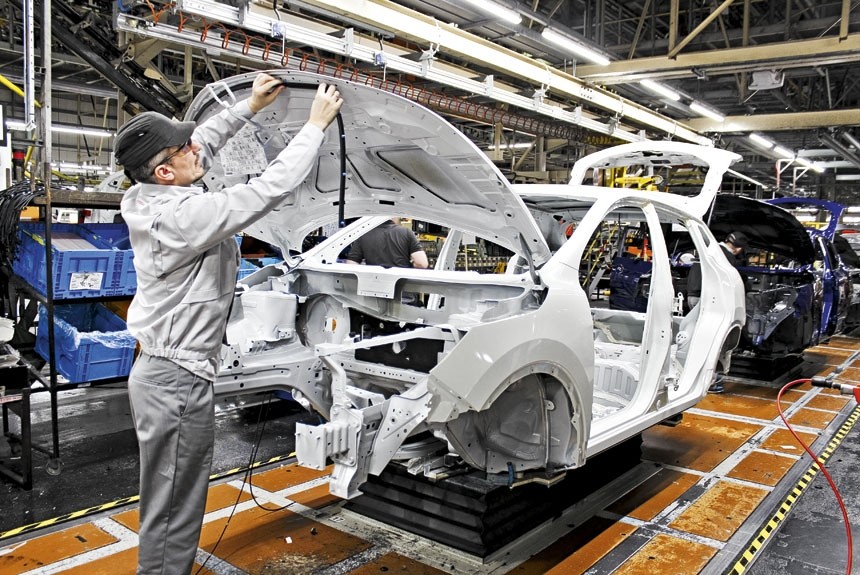
Я б в рабочие пошел, пусть меня научат! Например, собирать автомобили Nissan. На конвейере британского завода NMUK я и уплотнители капота ставил на Qashqai, и качество контролировал... Справился!
Не было бы счастья... Небольшой двухсоттысячный Сандерленд близ Ньюкасла-на-Тайне в Северной Умбрии мог бы так и остаться ничем не примечательным тихим провинциальным городком среди зеленых холмов с замшелыми замками. Но в начале 80-х в Северо-Восточной Англии грянул кризис: закрывались верфи и угольные шахты, резко пошла вверх безработица. И правительство тогдашнего премьера-консерватора Маргарет Тэтчер решилось призвать на помощь иностранцев: заключило контракт о промсборке автомобилей с процветающей компанией Nissan.
Японцы облюбовали военный аэродром под Сандерлендом. Летчиков переселили, землю выкупили, а на бывшем летном поле, оставив на память небольшой музейчик королевских ВВС, в 1984 году заложили завод NMUK — Nissan Motor Manufacturing UK. И в 1986-м с конвейера сошел первый Nissan Bluebird.
Уже через три года здесь же открылся региональный техцентр NTCE, Nissan Technical Centre Europe. Как раз тогда, в ноябре 1989 года, пала Берлинская стена. Случайность, конечно, — но сколь символичная с точки зрения новых рынков сбыта!
В 1991-м разросшийся NTCE переехал в технопарк в Крэнфилде, что в графстве Бедфордшир неподалеку от Лондона. Сейчас более 800 инженеров, технологов и конструкторов со всего света во главе с японцем Такаси Сиракавой разрабатывают или адаптируют здесь все предназначенные для Европы автомобили Nissan и Infiniti. Такие центры, к слову, есть в каждом ключевом регионе: помимо Японии и Европы это Южная Африка, Центральная и Южная Америка (в Мексике и Бразилии соответственно). Чем не глобальная паутина?
Чего не хватает для самодостаточности? Дизайна! Американские вкусы учитывает региональная студия в Сан-Диего, китайские — пекинская. А европейское отделение NDE, Nissan Design Europe, открыли в 2003 году в Лондоне. Там, где раньше были железнодорожные ремонтные мастерские, теперь под началом Коджи Нагано трудится команда из 75 дизайнеров, проектировщиков и моделлеров. Именно здесь создан, к примеру, экстравагантный Nissan Juke.
Что до самого завода, то в 1990-м Nissan Bluebird сменился на конвейере моделью Primera, в 1992 году добавилась Micra, затем Almera, а сейчас 6700 рабочих выпускают здесь Nissan Qashqai, Juke, Note и электромобили Leaf, а с 2015-го — Infiniti Q30. И на предприятии не просто штампуют, варят и красят кузова и собирают автомобили, а делают двигатели, отливают пластиковые и металлические детали... И даже производят блоки тяговых аккумуляторов для электромобилей. А по соседству — целый кластер подтянувшихся поставщиков: Valeo, Tacle, Calsonic Kansei, Hashimoto и Unipres.
В итоге немаленький NMUK вырос в лидера автоиндустрии Великобритании! Отсюда родом каждый третий из полутора миллионов сделанных в прошлом году на острове автомобилей, причем 80% из них идут на экспорт, включая российский рынок.
Для сравнения: Jaguar Land Rover тоже собирает без малого полмиллиона машин. Но не на одном, а на трех заводах.
Неудивительно, что NMUK под завязку набит роботами, манипуляторами и вспомогательными механизмами. Сварочное производство автоматизировано на 90% — включая даже подсборку модулей (на большинстве заводов, которые я посещал, это делают вручную). В малярном цехе, правда, наряду с роботами трудятся и люди, а используемые здесь материалы BASF не самые стойкие к агрессивным средам (АР №5, 2016). Не потому ли возникали вопросы к выносливости лакокрасочного покрытия у «английских» кроссоверов Nissan Qashqai (АР №8, 2014)?
Сборка образцовая. Полностью роботизированы только операции по нанесению клея на ветровое и заднее стекла и установка люков в крышу. Но механические помощники ассистируют при монтаже стекол и колес, снятии и навеске дверей, установке подвески и «свадьбе» кузова с силовым агрегатом, заправке автомобиля всеми нужными жидкостями... Предварительно собранные массивные передние панели автоматические руки монтируют в салон всего за две—три секунды, детали к сборочным постам доставляют тележки-роботы, и даже комплектовать «заказы» крупногабаритными деталями (например, подрамником) — тоже задача автоматики.
А главный помощник — сам конвейер, состоящий из движущихся платформ пола. Не нужно все время догонять кузов — стоя на месте, куда удобней работать с остовом будущего автомобиля, покоящимся на постаменте-домкрате (его высота своя для каждой из моделей).
Я в этом убедился лично. Облачение в фирменную серую рабочую униформу, короткий инструктаж — и вот я стою на одном из 84 постов нитки главного конвейера. Моя задача — установка уплотнителей на Nissan Qashqai. Знаете, чем светлые кузова отличаются от темных? С первыми проще работать сборщику: лучше видны монтажные отверстия!
Сперва я едва поспевал, и конвейер пару раз завозил меня вместе с черным кузовом на «территорию» следующей операции, где монтировали шумоизоляцию. Но затем втянулся — поводов для критики у контролеров не нашлось. А их тут предостаточно: после каждой восьмой операции чек-пойнт (всего их в конвейер «встроено» десяток), и огрехи сборки обычно находятся у пары автомобилей из каждой сотни.
Кстати, ниссановская производственная система суть тойотовская TPS со всеми ее атрибутами. И андон имеется. Правда, здесь это не шнур, а множество кнопок вдоль линии — на каждом сборочном посту. Нажал — и конвейер встал, а на смартфон мастера автоматически отправилось сообщение с номером проблемного участка.
А затем я и сам заделался чек-меном на посту контроля качества кузовов. «Полосатый» световой тоннель — самая первая из финальных проверок, за которой следует солидный список тестов: компьютерная диагностика всех систем, проверка тормозов, подвески, углов установки колес и регулировки фар. Каждый автомобиль разгоняется до 120 км/ч на беговых барабанах, мокнет четыре минуты в дождевальной камере и прогоняется по заводскому треку с разными видами дорог.
А на осмотр кузова — всего одна минута! Как успеть? И здесь есть свои маленькие хитрости: «пробежавшись» по зазорам дверей и крышки багажника, нужно повнимательнее обследовать «болевые» точки. На кузове кроссовера Qashqai это, к примеру, стык капота с крылом, а у электрокара Leaf — с кромкой облицовки бампера.
Наловчился я быстро — и даже нашел несколько огрехов. Но, повидав немало кривоватой установки кузовных панелей у сандерлендских Кашкаев прошлых лет, я ожидал худшего! Сборка явно стала аккуратней. Во многом потому, что в Сандерленде теперь делают и Infiniti, а у этой марки более жесткие требования к качеству.
Так что NMUK сейчас на подъеме, как и европейский рынок в целом. Поэтому рабочие в экспортоориентированном Сандерленде пашут в три смены. А вот в России…
В прошлом году Nissan смог продать у нас только 90877 машин, почти на 44% меньше, чем годом раньше. Из-за этого завод под Санкт-Петербургом (АР №1, 2010) оказался загруженным лишь на треть от своей мощности, выпустив 33 тысячи автомобилей. А теперь перешел в односменный режим, и до конца марта компания хочет сократить четверть из двух тысяч рабочих.
Но почему бы не загрузить российское предприятие заказами на экспорт? Потому что питерский завод изначально создавался только для нашего рынка: фактически — чтобы не платить пошлины благодаря знаменитому постановлению №166 о промсборке. Он относительно невелик и не столь автоматизирован, вокруг него нет внушительного кластера поставщиков комплектующих, уж не говоря про НТЦ и дизайн-студию. И запущен завод только в 2009 году.
А NMUK к тому времени работал уже более двадцати лет. Ведь, когда его открывали в середине 80-х, в СССР никто и предположить не мог, что под Ленинградом кому-то из иностранцев будет позволено строить свой завод! Тем более — вместо военного аэродрома.