Находим восковые фигуры на автозаводе концерна Volkswagen
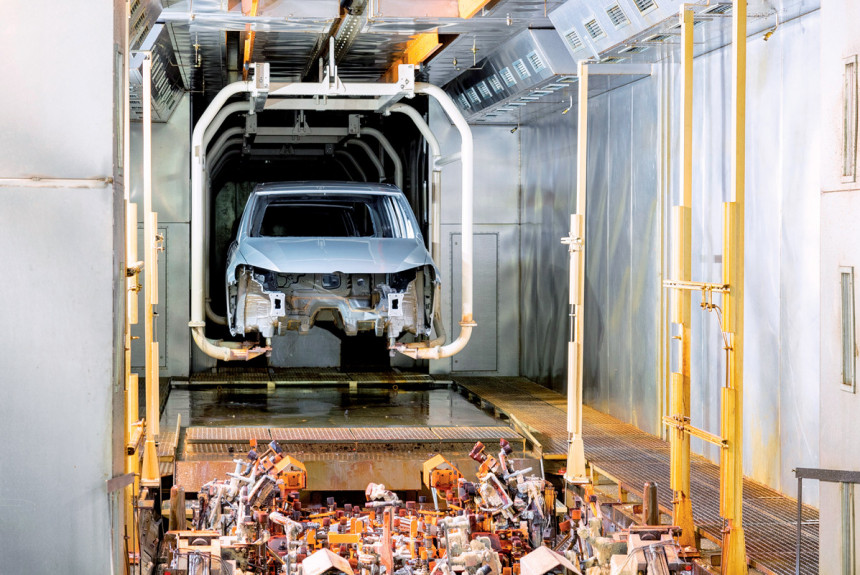
Угадаете, что общего между свечным заводиком отца Вострикова из «Двенадцати стульев» Ильфа и Петрова и любым автозаводом концерна Volkswagen? Воск и парафин. Такого мне видеть еще не доводилось: процедуру горячей заливки полостей кузова не практикует ни один другой автопроизводитель во всем мире!
Скользковатый пол, никаких резких запахов — и белые сугробы на технологической линии. Кузова на конвейерных креплениях приплывают сюда, в специальную часть цеха на заводе в Вольфсбурге, прямо из печки — разогретыми до +80°С. Затем целый рой маленьких роботизированных брандспойтов коннектится к технологическим отверстиям в нижней части кузова — и начинается закачка чистейшей с виду «воды». На самом деле это консистенция разогретого до +120°С парафина — меньше чем за минуту в кузов закачивается аж 360 литров! Разумеется, весь он там не остается, иначе легковушка весила бы как броневичок — такой литраж нужен, чтобы гарантированно пролить все нужные полости. Одна часть жидкого парафина тут же стекает обратно в резервуар под конвейером, а остатки, подостывшие до +75°С, сливают чуть позже, наклонив кузов назад под углом 15°. В итоге на металле от пары залитых бочек остается всего полтора литра парафина, на ощупь похожего на размягшее от воды белое мыло.
А затем чуть-чуть синтетического воска добавляется на внутренние поверхности боковых дверей, причем их даже не открывают: пара роботизированных рук с распылителями ювелирно проникает в салон через оконные проемы. А вот дверь багажника они игнорируют! И зря. Немцы считают, что вклеенное в нее стекло — это гарантированная защита от проникновения влаги, однако конденсат никто не отменял. Теперь ясно, почему пожилой Volkswagen если и начинает ржаветь, то именно с третьей—пятой двери.
Между лакокрасочным покрытием (грунт, базовая краска и лак) и цинковой поверхностью панелей еще есть фосфатный слой толщиной от 1 до 2 мкм и катафорезный грунт толщиной около 20 мкм. Большинство оцинкованных кузовных панелей автомобилей Volkswagen имеют толщину 0,8 мм
Впервые заливку воском Volkswagen начал практиковать еще во времена Гольфов и Пассатов первого поколения, с 1978 года. И если технологию нанесения покрытия с тех пор радикально преобразили роботы, то сами материалы революционных изменений не претерпели. Одним из достижений последних лет, к примеру, стало снижение рабочей температуры парафина на 5°С — ради экономии электричества.
Герметичная диодная подсветка заднего номера должна решить проблему с недолговечностью из-за коррозии
Важнее то, что воск и парафин лишь вишенка на антикоррозионном торте. Во-первых, для своих кузовов концерн VAG (равно как и Daimler с BMW) использует стальной прокат, с обеих сторон покрытый слоем цинка толщиной до семи микрон. Сэндвич лакокрасочного покрытия тоже один из самых толстых в индустрии — до 130 микрон (у азиатских автомобилей зачастую на треть тоньше). Хотя здесь за продукцией концерна VAG и водится главный кузовной грешок. В 1991 году вместе с полной гальванизацией кузова были введены в обращение краски на водной основе — и с проблемами адгезии ЛКП с цинком столкнулись еще те, у кого были Audi 80 и Volkswagen Passat поколения В4. С тех пор борьба за косметическую привлекательность пожилых экземпляров так и не прекращается.
У платформы MEB (Modularen Elektrifizierungsbaukasten) для электромобилей усилитель из прессованного алюминия отделен от горячекатаной оцинкованной стали порогов клеем и изоляцией болтовых соединений, а все полости тоже обработаны воском
А во-вторых, сражение с будущей ржавчиной начинается уже при проектировании кузова. Один из ярких примеров структурной защиты от коррозии — нынешний Volkswagen Golf и его двери. В их самой уязвимой части, завальцовке по нижней кромке, — целая оборонительная линия. Полости между металлом в сложенном S-образном фланце заполняет технический клей, одновременно создавая дополнительную прочность. А внешний стык запечатывается еще и поливинилхлоридным уплотнительным швом. Ну а поверх всего — тот самый вышеописанный воск (инженеры уверяют, что он со временем почти не теряет своих свойств). Так что дополнительный антикор здесь точно не потребуется.
Еще примеры? Передние крылья контактируют с порогами не напрямую, а через эластомер, причем для стыка просчитана и его вентиляция. Внутреннее пространство между крылом и передней стойкой заполнено жестким формованным полимерным элементом (запечатанным мягкими уплотнительными губками для звукоизоляции) с зазором, обеспечивающим быстрый отвод воды. Те секции днища, которые не укрыты от повреждений пластиковыми экранами, защищены антигравийным ПВХ-покрытием, которое распыляется в жидком виде. Причем в концерне не поленились математически смоделировать траекторию полета камней из-под колес — и самое тонкое покрытие наносят в задней части пола, а на пороги и переднюю часть ниши запасного колеса кладут потолще. Интересно, что передние брызговики не ставят по требованию дизайнеров и спецов по аэродинамике: те категорически против.
Ну а проверяется правильность всех решений «динамическими» коррозионными испытаниями. Мы в Авторевю по ходу нашего ускоренного ресурсного теста имитировали пять лет сопротивления ржавчине «статикой» — за 60 часов в камере с температурой +37°С, влажностью 95% и концентрацией соли 3,5%. Немцы же пытают свои автомобили гораздо жестче! Сперва для контроля развития коррозии так же наносят на кузовные элементы тарированные насечки краски до металла. И камера тоже есть. Концентрация соли, правда, чуть меньше — 3%, но температура в их парилке +55°С, влажность стопроцентная, а тест длится намного больше. И если мы для усиления эффекта просто открывали капоты, то на фольксвагеновском испытательном полигоне в Эре внутри автомобилей создают разрежение — при вакуумировании влажный соленый воздух всасывается во все щелочки. Педантичные немцы подсчитали, что каждый автомобиль съедает не то что пуд соли, а целых 68 кило!
Поэтому за полгода испытаний немцы заглядывают в будущее дальше нас — имитируют 12 лет жизни автомобиля (причем результаты анализируют столь тщательно, что в конце разбирают кузов на части, разнимая около тысячи точек сварки). В том числе и за счет «динамизма» своих испытаний. Подопытные машины наматывают километры по усыпанным гравием дорогам — как поодиночке, так и цугом (для усиления «обстрела» камнями передней части), прямо и с широкими скольжениями, пролетают через соленые ванны на высокой скорости, за счет разрежения обеспечивающей втягивание воды в каждый уголок и трещину днища. А больше всего любопытно упражнение, когда для усиления абразивного и коррозионного воздействия автомобиль проезжает через соленую смесь из грязи, глины и металлической пудры.
Интересная мысль для развития программы ускоренных испытаний Авторевю, не правда ли?