Чем живет завод корейской фирмы Sangsin Brake
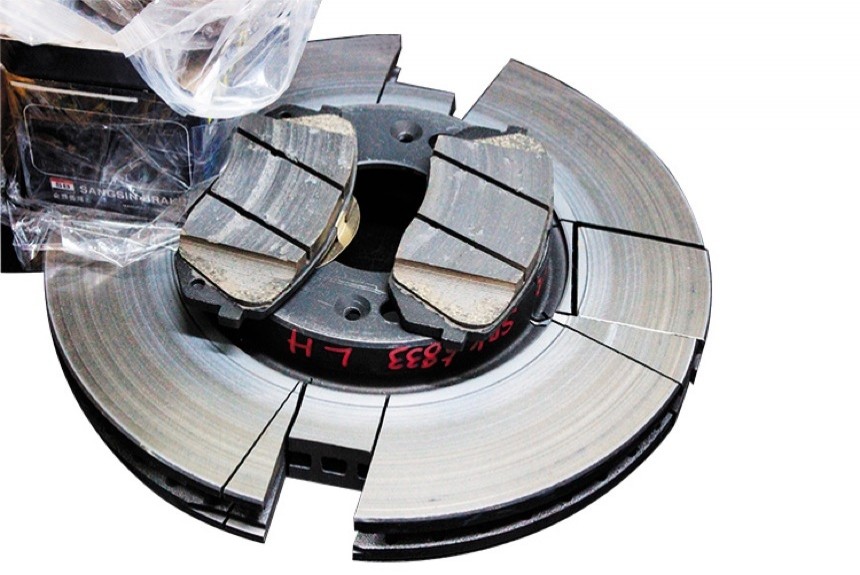
К тормозам корейских автомобилей у нас серьезных претензий пока не было - в сравнительных тестах с европейскими и японскими одноклассниками в «тормозных» дисциплинах они чувствуют себя вполне уверенно. Тем интереснее было слетать в Страну утренней свежести на завод фирмы Sangsin Brake: именно колодки с клеймом «SB» стоят на большинстве «корейцев».
Главный секрет тормозных колодок - в смеси, из которой сделаны накладки. Составить ее композицию - такое же искусство, как разработать пакет присадок для моторного масла. А когда я приехал в корейский город Тэгу, в исследовательский центр Sangsin Brake (его построили 12 лет назад по соседству с заводом, существующим с 1975 года), то убедился - «масляные» и «тормозные» лаборатории даже похожи, как сестры.
Люди в белых халатах, «кабинеты химии» с электронными весами и микроскопами, «классы физики» со спектрометрами различного действия, термоскопами и рентгеновскими установками… Есть мини-заводик для изготовления опытных экземпляров колодок, коррозионные, звукоизолированные и климатические камеры с температурой от -20 до +40°С с дождем и снегом и даже автомобильные стенды с беговыми барабанами и дистанционным компьютерным управлением. И парк тестовых машин - для отработки программы испытаний на шум, износ, «холодное» и «горячее» торможение.
Иначе никак - состав качественной фрикционной смеси (обычно в него входит до 30 элементов), в отличие от тех же масел, нельзя сделать универсальным для разных машин. Колодки приходится доводить под динамику и «весовую категорию» конкретной модели автомобиля, не забывая при этом об экономической составляющей, - искать компромисс между эффективностью торможения, износостойкостью и ценой. Поэтому формул смесей - сотни. Причем те модели автомобилей, для которых колодки поставляются на конвейер, Sangsin покупает!
Тестовый парк внушительный: колодки SB ставят на 80% корейских машин, в том числе на российские Kia и Hyundai. В Южной Корее Sangsin - крупнейшая «тормозная» компания, в мире - восьмая по величине. Причем Mando или Bosch не брезгуют перепаковкой колодок SB, продавая их под своими брендами. Для вторичного рынка Sangsin использует марки Hi-Q и Hardron - на них приходится 40% всей программы. А «на сторону» корейцы продают не только готовые колодки, но и полуфабрикат-порошок - контейнеры уходят в Европу, Америку, Японию, Индию, Китай…
Общая структура фрикционной смеси стандартная - это модификаторы трения, усилители, наполнители, абразивы и связующие, и все производители колодок используют схожий набор элементов. Но, к примеру, в качестве связующего элемента, своеобразного клея (20-40% смеси), в одних колодках применяется феноло-альдегидный полимер - бюджетный, но не любящий перегрева, а в колодках подороже - более стойкие полимеры, усиленные крезолом или бором.
Наполнителем, формирующим структуру накладки (15-35% смеси), когда-то служил асбест, популярность которого сошла на нет к середине 80-х годов, а в 1997 году он вовсе был запрещен - якобы из-за вреда для здоровья людей. До 2000-х годов были популярны «полуметаллические» колодки, содержащие 30-50% сплавов железа, меди, никеля, - главной претензией к ним было «жесткое» отношение к тормозному диску. Сегодня в почете керамическое или базальтовое волокно, материалы на основе силиката кальция или сульфата бария, слюдяной материал вермикулит и даже кевлар (Sangsin добавляет его в большинство колодок) - тот самый, что в «оборонке» используется для изготовления композитной брони.
«Керамика» (чем ее больше, тем накладка на вид светлее) хороша тем, что не сильно шумит, мало пылит и бережет тормозные диски, а главное - обеспечивает постоянство «чувства педали» даже при перегреве колодок. Однако долго прогревается, особенно зимой. Кевлар же более прочен и термостабилен, но меньше щадит диск и пыли от него больше - на пару с обычным графитом (5-15%), который обеспечивает существенную часть коэффициента трения.
Дорогой кевлар попутно придает большую износоустойчивость накладке, что позволяет меньше использовать еще сильнее истирающие тормозной диск усилители-металлы - те самые хорошо заметные «блестки» на поверхности колодки: сталь, медь и бронзу. Совсем отказаться от металлов пока не получается - они хотя и склонны вдобавок поскрипывать, но хорошо отводят тепло от тормозного диска, тем самым снижая риск его деформации при высоких температурах.
Но больше всего изнашивают тормозной диск абразивы (2-10% смеси) - тонкая во всех смыслах материя, и добро, и зло! В обмен на истирание диска смолотые в мелкий порошок кварц (по сути - песок), окиси алюминия, железа или силиката циркония, во-первых, обеспечивают начальную хватку в первый момент торможения, а во-вторых, очищают трущиеся поверхности (в том числе от ржавчины на диске) и поддерживают нужную шероховатость. Если абразива будет мало, диск быстро отполируется до зеркального состояния и тормоза заметно ослабеют.
Так как же при таком разнообразии фрикционных смесей выбрать правильные колодки взамен стершихся? Ведь если попадутся менее «цепкие» или с меньшим температурным диапазоном, возрастут усилие на педали и тормозной путь. А более «злые» колодки на автомобилях без АБС увеличивают риск блокировки колес и заноса, особенно на мокрой или скользкой дороге. Да и системы АБС настраиваются для работы с фрикционными характеристиками одной пары дисков и колодок - оригинальных.
И тут мы подошли к самому важному. Вопреки расхожему мнению купить «тот же оригинал, только с другим названием» невозможно! Оригинальные колодки со строго заданными характеристиками можно обнаружить исключительно в упаковке со значком автопроизводителя: у фирменных колодок и их «аналогов» для вторичного рынка под другим брендом, пусть и произведенных на одном и том же заводе, состав смеси различается минимум на 10-15% - таковы требования автокомпаний. В фирме Sangsin и не скрывают, что смесь у «сменных» колодок, как правило, проще. Конечно, сертифицированные неоригинальные колодки неопасны и в чем-то могут быть даже лучше «родных», но заводскую настройку баланса между величиной тормозного пути, характером работы АБС, термостабильностью, шумом, ресурсом накладок и дисков они в той или иной степени меняют.
Так что моя рекомендация - если нет желания экспериментировать, лучше покупать оригинальные колодки у дилера или в обычном магазине запчастей. Благо корейцы держат приемлемые цены - например, для Kia Sportage оригинальные передние тормозные колодки можно купить за 2000-2500 рублей, тогда как у его соперницы Тойоты RAV4 (АР №12, 2013) фирменные колодки оцениваются в 2800-3500 рублей, а обновить их на кроссовере Volkswagen Tiguan будет стоить 3000-4000 рублей.
Как делают тормозные колодки
1- Ингредиенты смешиваются вогромных миксерах, смесь выдерживается околосуток (чтобы прошли необходимые химические реакции между компонентами) иразделяется наточно отвешенные длякаждой колодки порции
1a - Пластину основы штампуют излистовой стали
2 - Из похожей нацемент смеси прессуют «куличики» поформе накладок испекают их вбрикеты нужной формы притемпературе около300°С
2a - Начисто обрабатывают поверхность пластины инаносят нанее клей
3 - Горячая накладка стыкуется с основой подвысоким давлением
4 - Собранная колодка на6-8 часов отправляется навулканизацию притемпературе 200°С
5 - Накладке придается окончательная форма, закругляются края ишлифуется поверхность
6 - Колодка окрашивается, наносится маркировка
7 - При необходимости приклеивается противоскрипная накладка иприклепываются пластины датчиков износа
8 - На выходе - контроль качества и упаковка