Юрий Ветров своими глазами увидел, как собирают суперкары Lamborghini
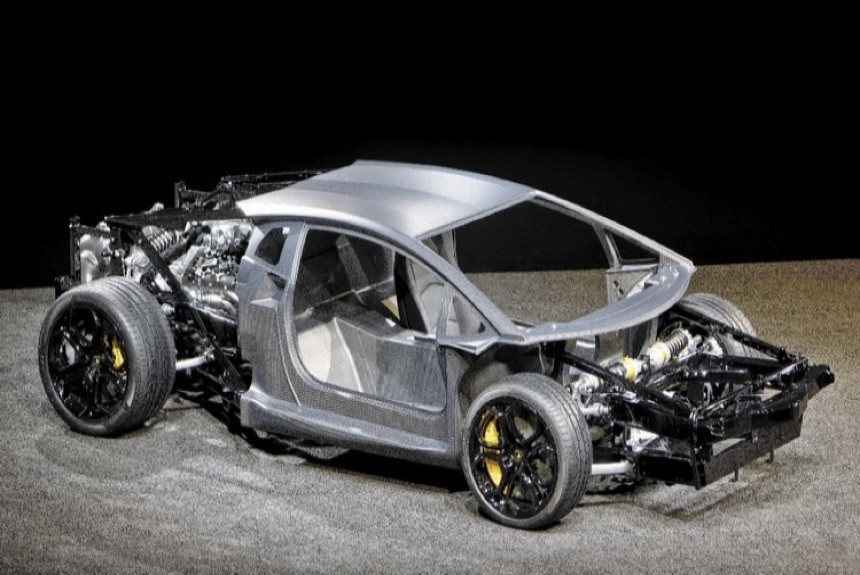
Улыбчивый итальянец аккуратно снимает полиэтиленовую упаковку с липкого углепластикового рулета, кладет черный комочек под десятитонный пресс... Ба-бах! Потом всего пять минут нагрева до 150 градусов Цельсия под давлением в 60 атм - и кронштейн готов.
На фирме Lamborghini «куют» углепластик! А начинается долгий процесс изготовления суперкара Lamborghini Aventador с... раскроя ткани.
Может быть, дело именно в революционной технологии «ковки» углепластика, как называют ее на Lamborghini по аналогии с изотермической штамповкой легкосплавных деталей?
В подчинении Лучано Тео, заведующего на заводе Lamborghini в Сант`Агате-Болоньезе композитной тематикой, семь инженеров и 34 рабочих - огромный штат для маленькой фирмы! Вдобавок Lamborghini уже несколько лет сотрудничает с Вашингтонским университетом и с компаниями Callaway Golf и Boeing. Тео с гордостью демонстирует «кованые» углепластиковые рычаги подвески от концепт-кара Sesto Elemento - мол, глядите, какой прорыв в технологиях!
Действительно, метод, схожий с изотермической штамповкой, позволяет делать углепластиковые детали быстрее и дешевле. Но - об этом Тео говорит неохотно - для высокопрочных композитных деталей крайне важна точность ориентации углеволокон. А при «ковке» обеспечить ее просто не получается! Ведь в качестве сырья нельзя использовать пропитанную ткань или полосу - только «сырую» массу с хаотично расположенными отрезками волокон. Так что пока эта технология подходит лишь для концепт-каров или для второстепенных, малонагруженных деталей. Не зря для Авентадора «куют» только несколько кронштейнов и эмблемы, а рычаги подвески серийной машины сделаны из алюминия.
Но «ковка» - далеко не единственная интересная технология в Сант`Агате.
Как обычно делается монокок? В течение нескольких часов рабочие вручную выкладывают в форму маты из углеродной ткани, пропитанной связующей смолой. Потом устанавливают закладные элементы (резьба в композите резко снижает прочность и быстро изнашивается, поэтому используют стальные или алюминиевые элементы креплений), а затем готовая конструкция несколько часов «запекается» в автоклаве. В Lamborghini остроумно решили разделить монокок на несколько подсборок. Часть элементов будущей «скорлупы» производят на линии, где «сухие» маты (без связующего) укладывают в пресс-формы, в которые потом закачивается полимер. Другие, более тонкостенные детали, делают методом вакуумного формования: гибкая оболочка под действием разрежения обжимает материал на оправке. Для этого метода нужен особый материал - со связующим компаундом, который «схватывается» при температуре всего 50-60 градусов Цельсия. Его хранят в специальных холодильниках при 18-градусном морозе - иначе он слипается!